SOLUTION GLOBALE DE RECRUTEMENT - Embauche simplifiée, talents sans conseil
Langue du site

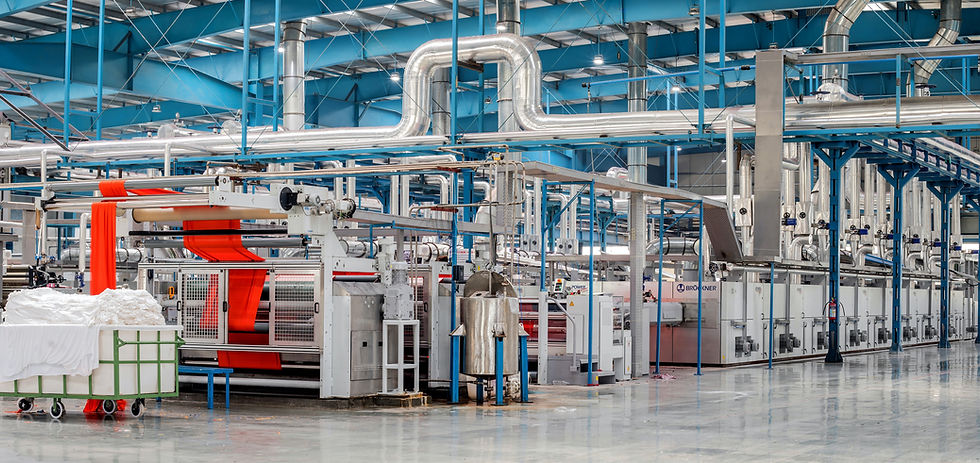
Aaron Walker
8 déc. 2024
Le secteur manufacturier est confronté à une demande importante de compétences dans les domaines de l'ingénierie et de l'exploitation. Cette pénurie est due à une combinaison de facteurs tels que le vieillissement de la main-d'œuvre, les avancées technologiques et l'évolution des exigences législatives. Principales tendances à l'origine de la demande :
Aperçu par la Skills Coalition
Le secteur manufacturier est confronté à une demande importante de compétences dans les domaines de l'ingénierie et de l'exploitation. Cette pénurie est due à une combinaison de facteurs : vieillissement de la main-d'œuvre, progrès technologiques et évolution des exigences législatives. Principales tendances à l'origine de la demande :
Technologies avancées :
Il existe un besoin croissant de compétences en automatisation avancée, en robotique et en Internet industriel des objets (IIoT). Les ingénieurs compétents dans ces domaines sont essentiels à l'heure où les processus de fabrication sont de plus en plus numérisés et automatisés
Développement durable et ingénierie des matériaux :
L'accent législatif étant davantage mis sur la durabilité, il existe une forte demande d'ingénieurs capables d'innover avec des matériaux et des processus respectueux de l'environnement. Cela inclut des compétences en analyse du cycle de vie et en processus de recyclage,
Gestion de projet et Lean Manufacturing :
Il est plus important que jamais de savoir gérer efficacement des projets, notamment dans le cadre de la production allégée. Il s’agit notamment de mener des projets qui améliorent la qualité tout en réduisant les coûts et le gaspillage.
Défis et solutions :
· Vieillissement de la main-d’œuvre et transfert de compétences :
· Une part importante de la main-d'œuvre qualifiée approche de l'âge de la retraite, ce qui risque de provoquer une perte des connaissances et de l'expérience accumulées. Il est urgent de transférer ces connaissances aux nouveaux venus dans le secteur.
· Lacunes dans la formation technique : Le rythme rapide des changements technologiques a dépassé les programmes actuels de formation et de développement, ce qui a conduit à un manque de compétences techniques nécessaires parmi les nouveaux travailleurs【92†source】.
Stratégies pour combler le déficit de compétences :
· Perfectionnement et reconversion : les entreprises se concentrent sur la formation de leur personnel existant pour qu'il puisse maîtriser les nouvelles technologies et les processus de fabrication avancés. Cela inclut à la fois les compétences numériques et les compétences générales telles que la pensée critique et la résolution de problèmes.
· Partenariats public-privé et apprentissage : pour remédier durablement à la pénurie de compétences, les fabricants concluent des partenariats avec des établissements d’enseignement et des programmes gouvernementaux. Cela permet d’élaborer des programmes d’études plus adaptés aux besoins de l’industrie et de mettre en place des programmes d’apprentissage solides.
· Tirer parti des effectifs partant à la retraite : Certaines stratégies incluent l’utilisation de l’expertise des employés partant à la retraite pour encadrer les nouvelles recrues, garantissant ainsi que les connaissances et les compétences essentielles sont transmises efficacement.
L’industrie manufacturière doit continuer à s’adapter en élaborant une planification stratégique de la main-d’œuvre et en s’engageant dans une formation continue pour suivre le rythme des avancées technologiques et des changements législatifs. Cela permettra non seulement de combler le déficit actuel de compétences, mais aussi de préparer le secteur aux défis et aux opportunités futurs.
Découvrez plus d'informations et de ressources d'experts sur Skills Coalition . Que vous cherchiez à rester en tête des tendances du secteur, à améliorer votre carrière, à enregistrer votre CV et à consulter les postes ouverts . Si vous cherchez à embaucher les meilleurs talents, notre plateforme dispose des outils et des connaissances nécessaires pour vous accompagner dans votre parcours. La Skills Coalition simplifie le recrutement. Des talents sans frontières .
Les domaines de recrutement spécialisés comprennent : Finance et comptabilité , aérospatiale et sciences spatiales , biotechnologie , cybersécurité , données et analyses , technologies de l'information , apprentissage automatique et IA , fabrication , produits pharmaceutiques , énergies renouvelables , ventes et marketing . Cliquez sur l'un des liens pour en savoir plus sur les emplois de recrutement et l'embauche dans ces domaines.